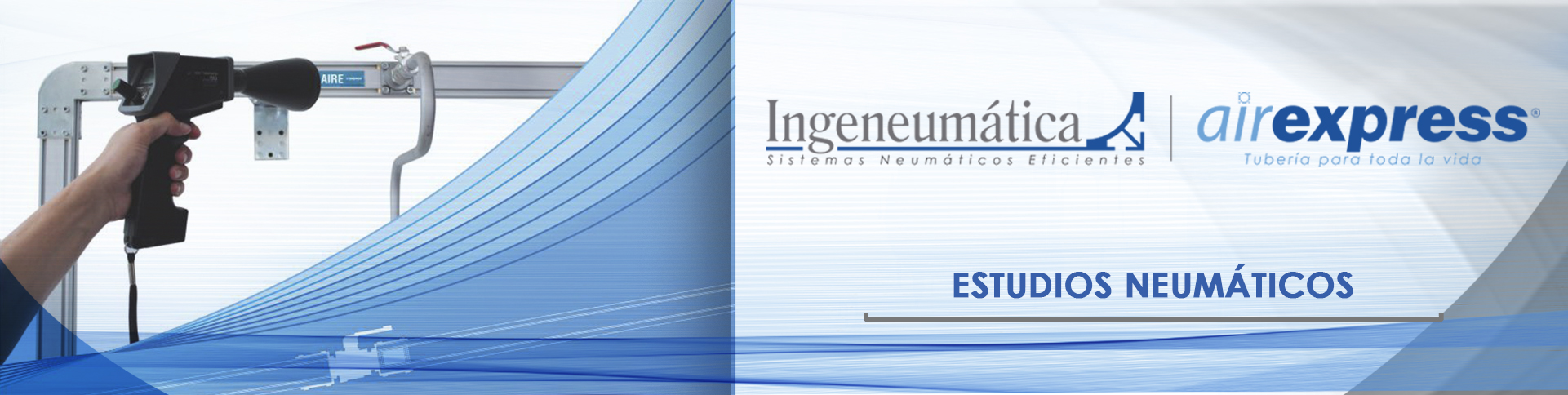
La medición es la clave fundamental para determinar qué se puede mejorar.
Si desea conocer cómo puede hacer más productiva y ecológica su empresa no dude en contactarnos.
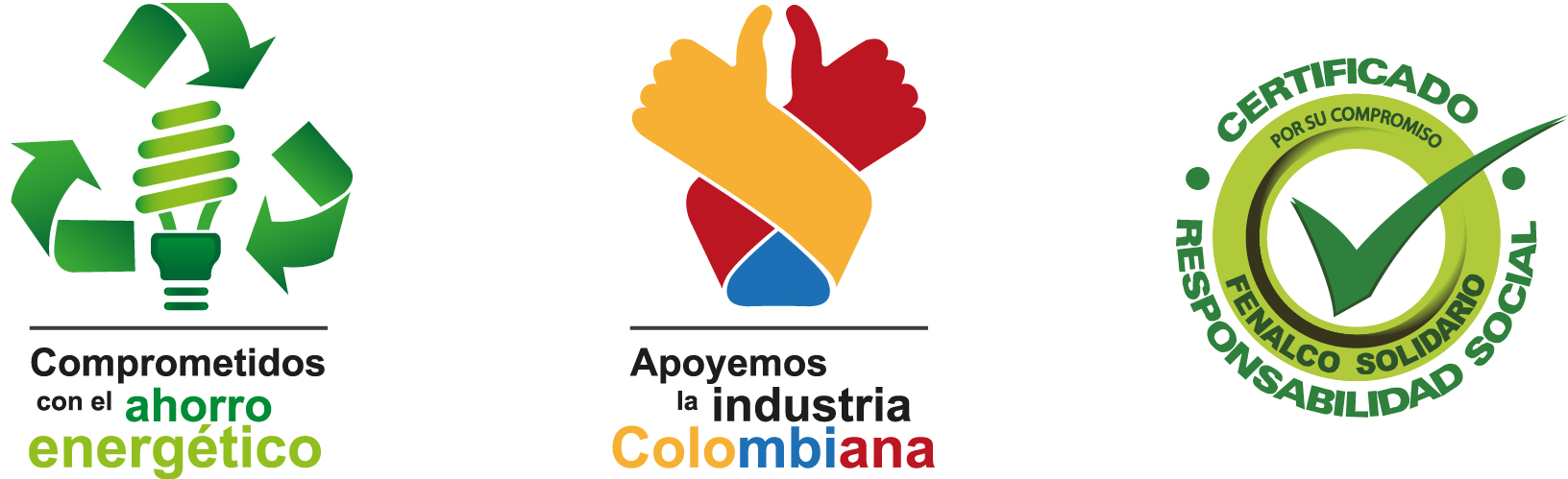
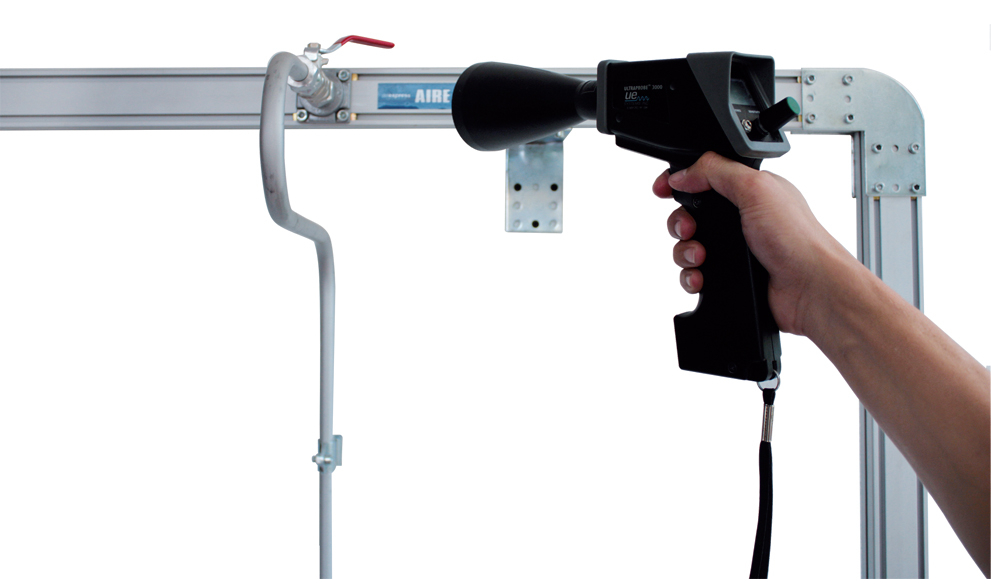
Detección de fugas
Se realiza por medio de un dispositivo ultrasónico y se marca en una etiqueta, para llevar un control sobre las fugas.
Información obtenida:
- Listado de las fugas encontradas.
- Identificación de cada sitio de fuga.
- Informe cuantitativo del desperdicio por fugas según la capacidad de aire comprimido instalada en la planta.
Sistema de monitoreo de demanda del aire
Elementos diseñados para registrar el funcionamiento de los compresores, tomando registros de la demanda de la planta y de la presión del aire en el sistema, con un promedio de medida móvil, para obtener las curvas reales de su comportamiento en el tiempo.
Información obtenida:
· Porcentaje de trabajo de los compresores de acuerdo con la demanda.
· Medición de la demanda de aire comprimido en la planta.
· Comportamiento de la presión del sistema en el tiempo.
· Determinación de los momentos picos de demanda de aire en la planta.
· Evaluación de los posibles errores que se puedan cometer al momento de trabajar los compresores, de acuerdo con la demanda.
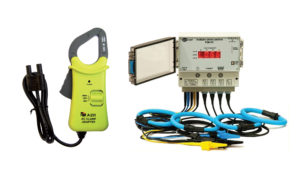
Medición del consumo de energía
Se instala una pinza amperimétrica en la acometida eléctrica al motor de cada compresor, que proporciona Factor de Potencia, Potencia Trifásica Activa y Potencia Aparente.
Información obtenida:
· Consumo de energía en kW, tanto en carga como en vacío, durante el tiempo analizado.
Medición del flujo entregado por cada compresor
Instalación del equipo a la descarga del compresor, para obtener CFM reales a 100 PSIg de presión, así como la Potencia Activa trifásica.
Información obtenida:
· ACFM reales entregados por el compresor a 100 PSIg de presión.
· Potencia Activa Trifásica real del compresor.
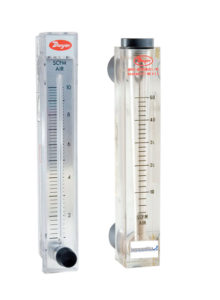
Medición del flujo por máquina
Medición directa con rotámetro o cálculo del consumo de los cilindros, obteniendo consumo real en CFM de la máquina o elemento neumático.
Información obtenida:
· Consumo real en CFM de la máquina o elemento neumático.
Diagnóstico del estado de la red neumática
Recorrido por toda la instalación neumática analizando cada uno de los siguientes aspectos:
· Presión.
· Calidad del aire (Sistema de filtrado según ISO 8573:1).
· Inclinación de la red.
· Conexiones.
· Accesorios de línea.
· Trampas de condensación.
· Sala de Compresores.
· Tomas a máquinas y de servicio.
Información obtenida:
· Una vez terminados los pasos anteriores, se darán las recomendaciones más importantes para mejorar la red actual.
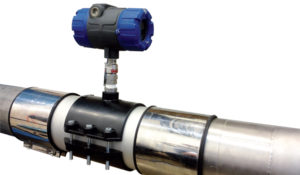
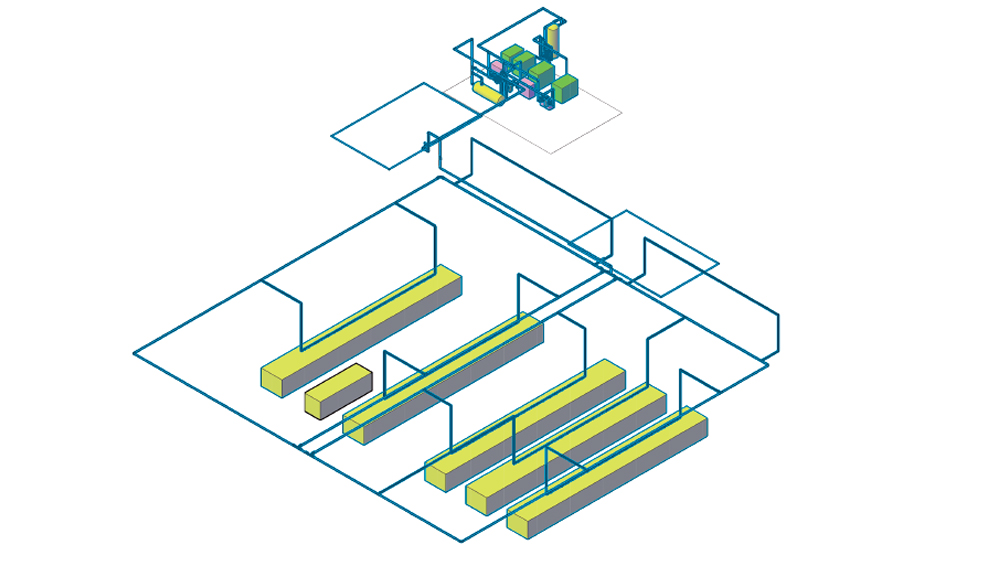
Rediseño de la red
Recorrido por toda la instalación neumática, para analizar su estado y obtener:
· Cálculo del diámetro óptimo de la red principal y de la red de servicio.
· Rediseño de la red neumática, teniendo en cuenta el consumo real de la planta, las caídas de presión y la distribución óptima de conexiones y drenajes.
· Entrega del plano de la red nueva, teniendo en cuenta las recomendaciones técnicas. Corrigiendo las deficiencias encontradas en la red actual, tales como sala de compresores, conexiones, ubicación de drenajes, inclinaciones de la red, entre otros.
NOSOTROS
Ingeneumática S.A.S. Es una empresa dedicada a diseñar, desarrollar, producir y comercializar redes de aire comprimido, así como automatización industrial; representando una solución integral en sistemas neumáticos a través de la innovación para todo tipo de industrias, satisfaciendo a nuestros clientes con servicios oportunos y contribuyendo paralelamente al desarrollo de todos los que hacen parte de ella.
LINKS
NUESTRA NUEVA UBICACIÓN
• Carrera 55B # 72A-94
Itagüí, Antioquia, Colombia
- (+57 604) 448 8836
- (+57) 314 890 9672 / (+57) 314 890 9668
- comunicaciones@ingeneumatica.com
- division.tuberia@ingeneumatica.com / (+57) 321 6409937
- division.maquinas@ingeneumatica.com / (+57) 314 890 9662
www.ingeneumatica.com